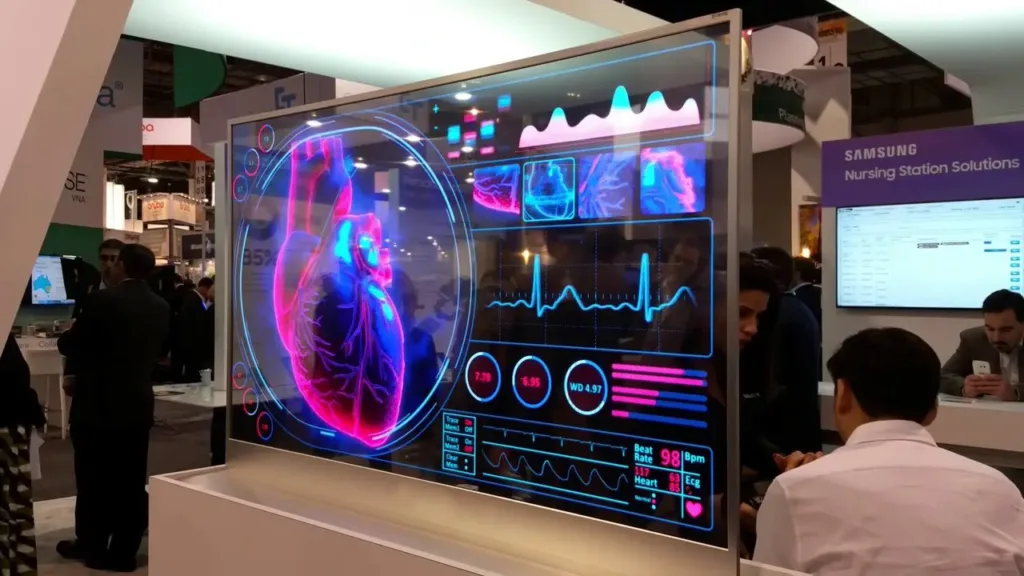
How to make a transparent OLED screen? In-depth analysis of Yoda factory’s core technology
Author:Yoda . 4/28/2025
In the field of digital signage, transparent OLED screen are improving commercial display forms with disruptive display technology. As a digital signage manufacturer focusing on the global market for many years, Yoda has provided more than 1,500 customized solutions for more than 30 countries around the world with its self-developed transparent display technology. This article will deeply analyze the entire manufacturing process of transparent OLED screens and share cutting-edge application cases in the industry.
The underlying technical architecture of transparent OLED screen
The core innovation of transparent OLED screen lies in achieving a dynamic balance between luminous efficiency and transmittance. Yoda adopts a multi-layer stacking structure design: on an ultra-thin substrate with a thickness of only 0.1mm, key components such as transparent anode (ITO), organic light-emitting layer (EML), and transparent cathode (Ag/IZO composite layer) are constructed in sequence. By optimizing the material ratio of the electron transport layer (ETL) and the hole transport layer (HTL), Yoda Laboratory successfully increased the screen transparency to 42%, while maintaining the excellent performance of 1000nits peak brightness and 120Hz refresh rate.
Compared with traditional LCD technology, Yoda transparent OLED screens has higher advantages: its self-luminous characteristics eliminate the need for backlight modules, reducing the screen thickness by 85% to 0.8mm; each pixel’s independent light control technology achieves an ultra-high contrast ratio of 1,000,000:1, maintaining clear visibility even in direct sunlight; the double-sided display function supports the superposition of virtual and real images, creating an immersive interactive experience for digital signage. Actual measured data shows that the 55-inch Yoda transparent screen has a 22% lower energy consumption than similar products in 30% transparency mode, and its service life exceeds 50,000 hours.
Detailed explanation of the entire manufacturing process of Yoda transparent OLED
Phase 1: Ultra-precision substrate processing
As the core carrier of the screen, Yoda uses ultra-white glass (transmittance 92.5%) as the substrate, and uses a magnetron sputtering process to plate a 150nm thick ITO conductive layer, with a surface resistance controlled within 8Ω/sq. The substrate needs to go through 18 cleaning processes, including megasonic cleaning (frequency 950kHz) and plasma activation treatment (power 300W), and the final cleanliness reaches ISO Class 5 standard, with surface particles ≤5/㎡.
Phase 2: Nanoscale organic layer deposition
In an ultra-high vacuum environment of 10⁻⁶ Pa, the precision metal mask (FMM) technology is used for material evaporation:
The accuracy of this process is required to reach ±1.5μm, and each 55-inch screen needs to complete more than 12 million precise positioning times.
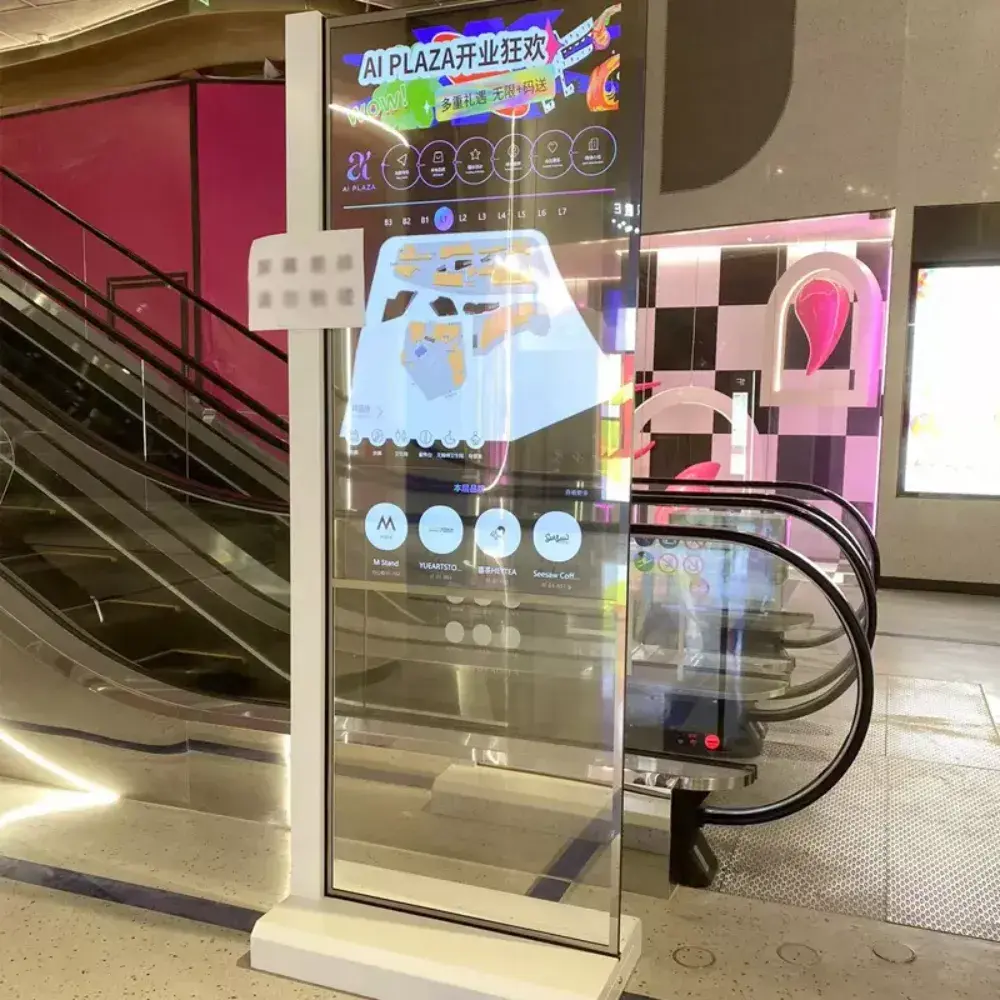
Phase 3: Triple protection packaging process
To solve the water and oxygen sensitivity problem of transparent OLED, Yoda has developed a new patented technology:
1. The inner layer is deposited with a 200nm silicon nitride (SiNx) film, and the barrier efficiency is 3 times higher than the traditional solution
2. The middle layer uses UV-cured epoxy resin to bond a flexible water-blocking film (WVTR<5×10⁻⁶ g/m²/day)
3. The outer layer is laser-welded with a stainless steel frame, and the impact strength reaches IK10 level
After 85℃/85%RH accelerated aging test, the screen life is extended to 35,000 hours after packaging.
Phase 4: Intelligent drive system integration
Yoda’s self-developed drive system supports:
The system is compatible with Android/Windows/Linux platforms, and built-in Yoda Cloud for remote content management.
Strict quality control and certification system
Yoda has established a four-dimensional quality assurance system:
The optical laboratory is equipped with Konica Minolta CS-2000 spectroradiometer to detect color gamut coverage (98% DCI-P3), brightness uniformity (ΔE≤1.5), and viewing angle deviation (color difference within 178° range <3 JNCD). The environmental test chamber can simulate complex conditions such as extreme temperatures of -40°C to 85°C, 95%RH humidity, and salt spray corrosion. After 1,000 hours of continuous operation, the power attenuation is less than 3%. The mechanical laboratory conducts 20G acceleration shock tests and 5-500Hz vibration spectrum analysis to ensure compliance with the IEC 60068-2 standard. The Energy Efficiency Center has passed the Energy Star 8.0 certification, the standby power consumption of the 55-inch screen is less than 0.5W, and the operating energy efficiency ratio reaches 1.2cd/W.
Six major industry solutions
1. Digital upgrade of luxury retail
2. Intelligent traffic information interaction system
3. Transparent presentation of medical images
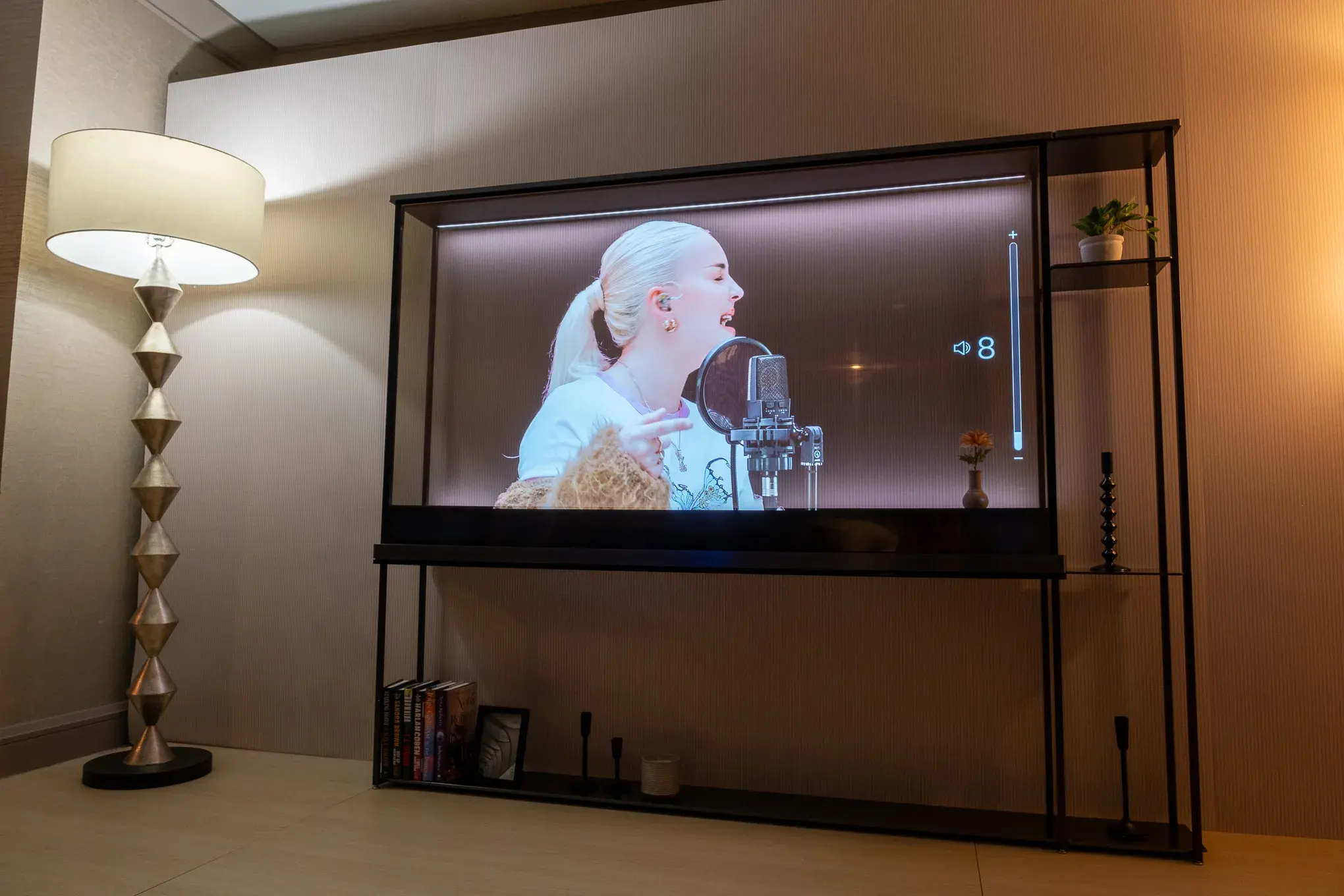
Four core competitiveness of Yoda
1. Deep customization capability
2. Patent technology cluster
3. Global service network
Technology evolution and future prospects
According to Yoda Research Institute’s “2025 Transparent Display Technology White Paper”, the industry will present three major trends: using graphene transparent electrodes to make the transmittance exceed 70%; micro-LED and OLED hybrid technology to achieve 2000nits brightness; if you need to obtain customized transparent OLED screen solutions, please visit the official website to check the latest technology white paper, or contact our international business team to obtain exclusive quotation solutions.